MICRONOR APPLICATIONS
Rotary Encoder
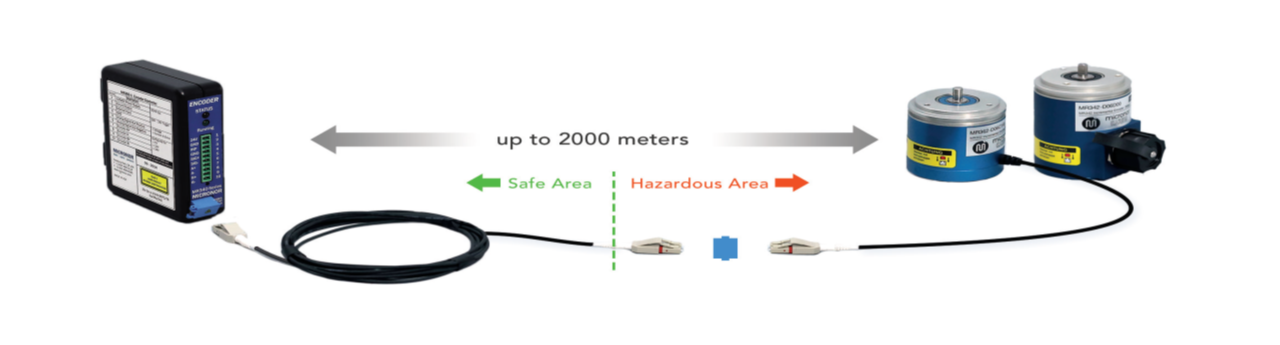
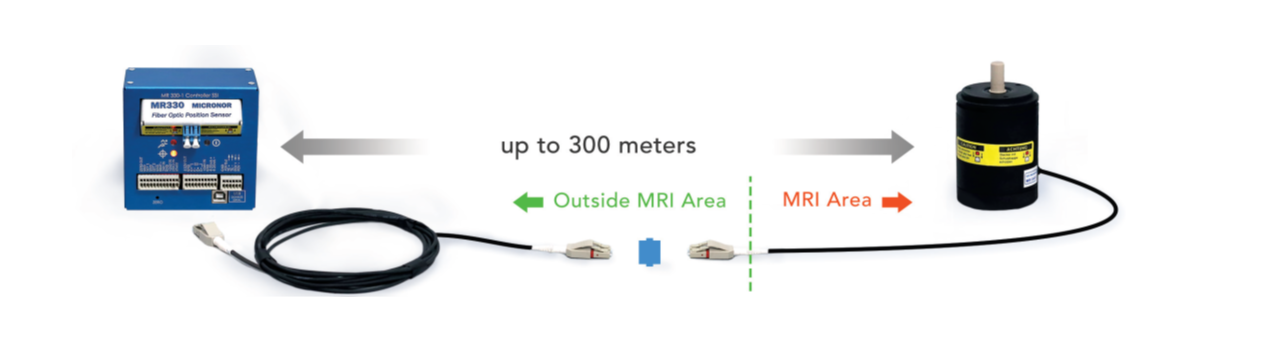
3-axis acceleration measurement at the tip of the 40m long wing
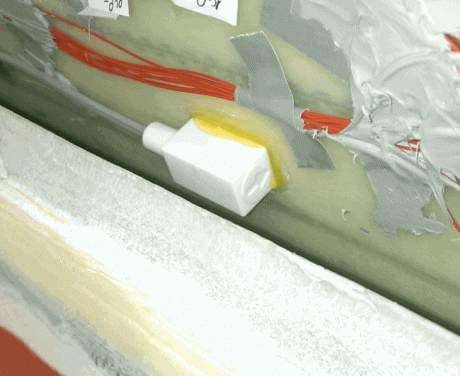
wind power and the optimization of the system can be ideally solved with the micronor fiber optic sensors.
The sensors are passive, so no battery or copper cable to the sensor, just glass and photons.
The distance from the sensor to the signal conversion can be 200m or more and that without losses.
Whether it is about acceleration in the wing, in the warehouse or in the generator, passive sensors are the ideal solution.
Whether it is about temperature measurement as a single point or as a multipoint, we offer the entire product range.
Compact FBG (Fiber Bragg) or Fabry Perot sensors complete our wind range, ask us.
End winding monitoring with the MICRONOR fiber optic acceleration sensors
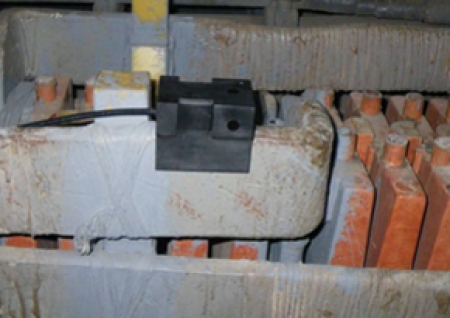
Monitoring large generators in operation is a "MUST" in order to preserve the large investment and to increase reliability.
With sensors, this large machine can also be operated in the optimal usable area; sensors are very important for this. Sensors
that can reliably measure even under high voltage and the general conditions in the generator.
The MICRONOR fiber optical acceleration sensors meet this requirement as they are 100% non-metallic, passive ..... fiber optic.
Due to the compact design, the acceleration can be recorded in the generator winding 1, 2 or 3 axes.
The sensor can be used safely in the temperature range from 0 ° C to + 200 ° C.
The sensor fulfills Class A but also Class F (155 ° C).
The frequency range is from 0.5 ... 1000Hz and has an output signal of 100mV / g and an acceleration range of + - 50g.
Fiber optic pantograph sensors for the ETR1000
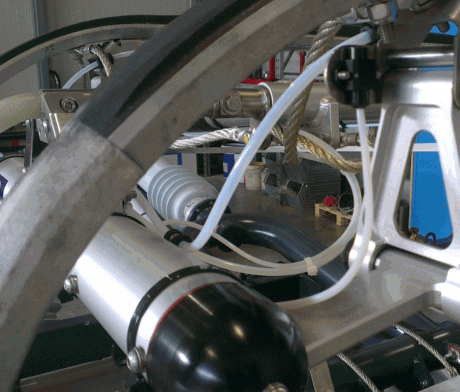
The MICRONOR fiber optical acceleration sensors are optimized for the pantograph application
and have been tested in use for several years.
The very light sensor is one thing for reliable operation,
but the entire wiring from the pantograph to the interior of the car and all connector transitions are also central.
Only with our over 30 years of experience in optical cabling in a robust "rolling stock" environment
could this task be reliably solved.
With new products such as the ETR1000, the sensor is delivered to one factory,
the cabling to the other and the electronics to be integrated into the overall system.
But in the end, in the final assembly, everything has to work plug and play. MICRONOR has this experience with fiber optic sensors.
The system is 100% passive, the sensor weighs max. 8g, is insulation-proof, has a high linearity over the entire frequency range from 0.2Hz to 400Hz and an extremely low noise behavior, stop fiber optic.
Fiber optic acceleration measurement on the pantograph
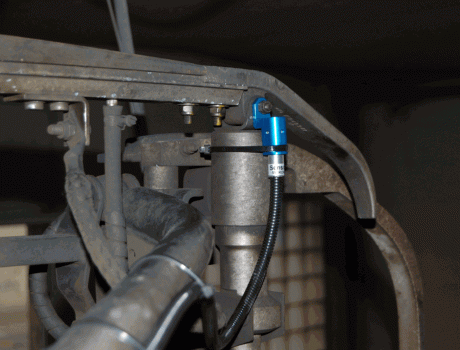
The 1-axis fiber optical acceleration sensors from MICRONOR were developed for pantograph diagnostics.
Through intensive tests in the laboratory, the sensor was tested by our customer up to speeds of 400km / h and + -50g.
Compared to all standard sensors, the 100% passive technology has the great advantage that the noise ratio is extremely low,
no power supply is required at the sensor and the signal transmission is passive and therefore very simple.
Fiber optical temperature measurement on high voltage cables
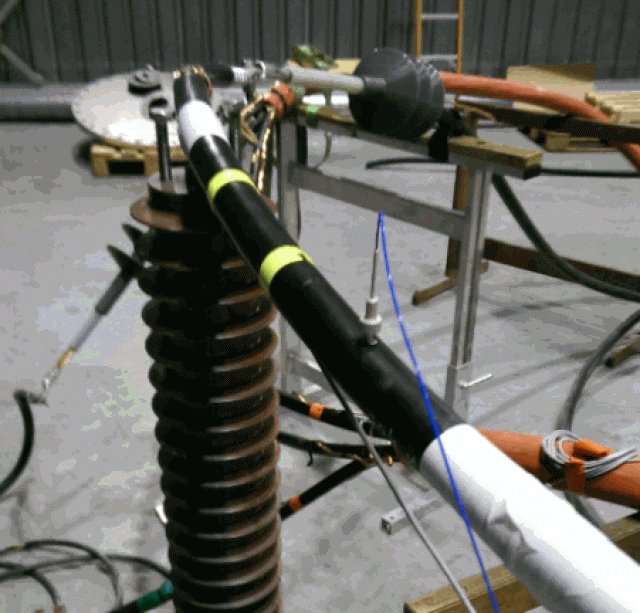
The temperature measurement in the high-voltage environment is not easy and involves dangers from earth loops and interference.
With the fiber optic temperature sensors from MICRONOR, the temperature can also be measured on live electrical conductors
without the risk of earth loops.
In addition, the signal is transmitted passively from the sensor to the electronics.
The evaluation electronics can be installed in the safe area.
Thanks to the wide range of extension cables and distribution systems.
A large selection of sensor tips and shapes enables the probe to be placed in almost all possible places.
Fiber optic lift measurement on the pantograph
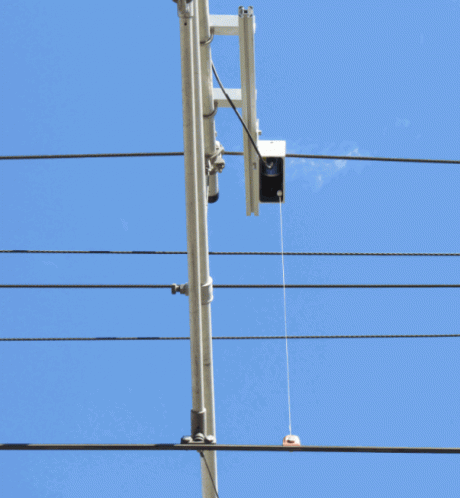
The MICRONOR uplift measuring system is a complete kit consisting of the uplift position measuring system,
the cabling on the mast, the connection box, the floor cable or underpass cable up to the optical-electrical conversion.
The system has been in use worldwide for years to measure the lift of the contact line by the passing pantograph.
This data can be recorded via Motbus-IP or USB or simply as a + -10V signal and forwarded to a control center.
Especially to detect defective pantographs at an early stage and to remove them from traffic
so that they do not damage the catenary even more and lead to catenary faults.
Railway infrastructure diagnosis is very important as a preventive measure and allows you to save a lot of money.
Fiber optic feedthroughs from MICRONOR
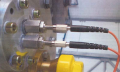
The MICRONOR fiber feedthroughs have been in use at CERN for many years.
Whether for a single mode or multimode fiber, we have the solution.
We prefer to use the DIN standard connector, solutions with FC-PC or ST are possible.
The bushings can also be used in ATEX Group II cat 2GD IP66.
Gear limit switches for MIL applications
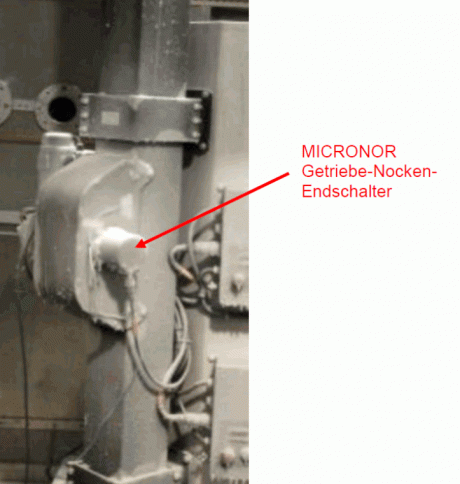
The MICRONOR geared cam limit switches are an ideal addition to military vehicles.
As an add-on or security element to the installed board systems.
Major manufacturers worldwide rely on our robust switches.
ice test according to MIL-STD-810C meth. 521.5 or
shock test according to MIL-STD-810G,
the devices with stand this environmental test.
Microswitches, cables and flange sockets all comply with the MIL standard.
Gear cam limit switches of the FRL90 series on the SEW gear unit
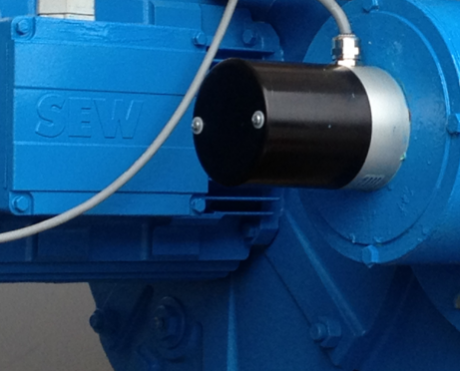
We have been producing MICRONOR geared cam limit switches for over 50 years.
Over the years we have continuously developed the devices and adapted them to new requirements or built new devices.
Over the years, a large range of geared cam limit switches has been created that fit into almost every application.
Whether it is a cam switch device for the bridge of a sea ship or in a Chilean mine or on a wheel excavator in Cotbus
or in stage technology or on a large ventilation fan with SEW motor in Sweden ... MICRONOR has the solution.
We also supply replacements for devices from our competitors that no longer manufacture them.
Gear limit switch on the crane drum
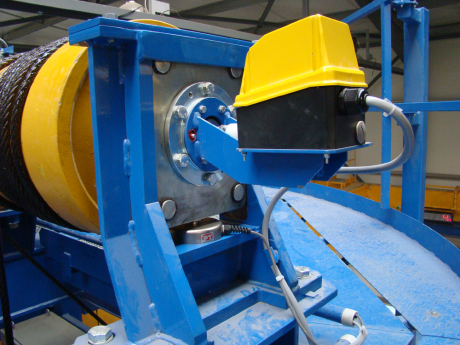
The MICRONOR gear cam limit switch in a PBT plastic housing with worm gear is ideal for mounting directly on the rope drum.
With a reduction of 100: 1, input shaft to the cams and adjustable double cams, a large stroke range can be covered.
The microswitches 10A 250V AC or 6A 24VDC with gold contacts can be used in a wide range of applications.
The microswitches have screw connections for direct wiring.
With the metric cable bushing, the device can be used in the IP 65 environment according to EN60529.
The gear limit switch can be supplied with 5 switching levels as double cams or single cams.
TWK-ELEKTRONIK APPLICATIONS
Wind Energy
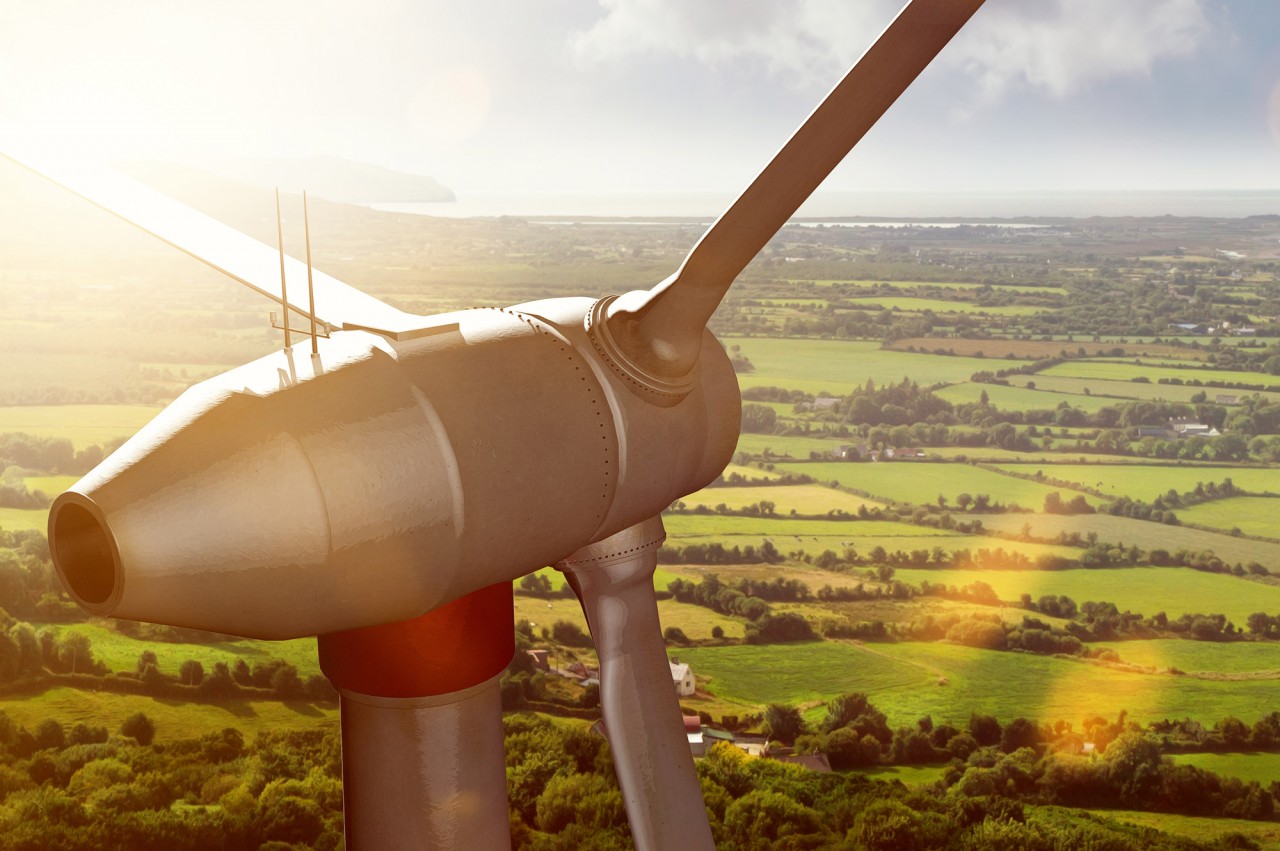
The generation of electricity using wind energy has now been established for over 20 years.
The wind energy industry can look back at an accordingly long and successful period of time.
And this industry's future prospects remain outstanding.
Technical further development of the systems has constantly increased their efficiency and operational reliability.
The requirements made on the sensor systems - e.g. rotary encoders - have increased accordingly.
TWK-ELEKTRONIK has been part of this development from the very beginning.
Germany's first major wind turbine - GROWIAN - for instance was equipped with an absolute rotary encoder from TWK. Since then,
TWK has been an important supplier to well-known companies within the wind energy industry.
Agricultual Machines
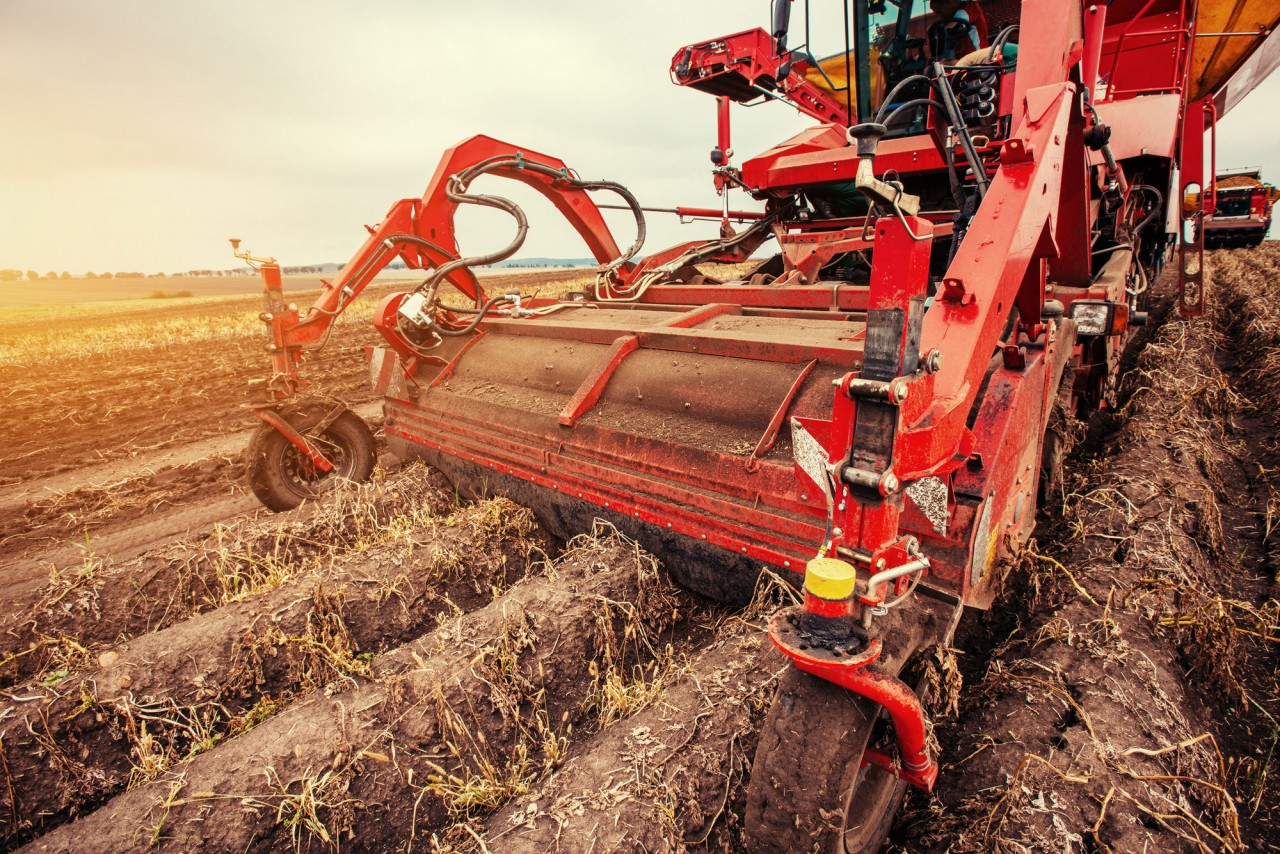
As is the case with construction machines, the level of automation is also constantly on the increase in agricultural machines.
Automated steering systems, driver support systems or sensor-controlled fertilisation are already integrated
as standard in modern agricultural machines.
Reliable and precise sensors form the basis for machine automation.
TWK-ELEKTRONIK supplies agricultural machinery manufacturers with magnetic rotary encoders and inclinometers.
Construction Machines
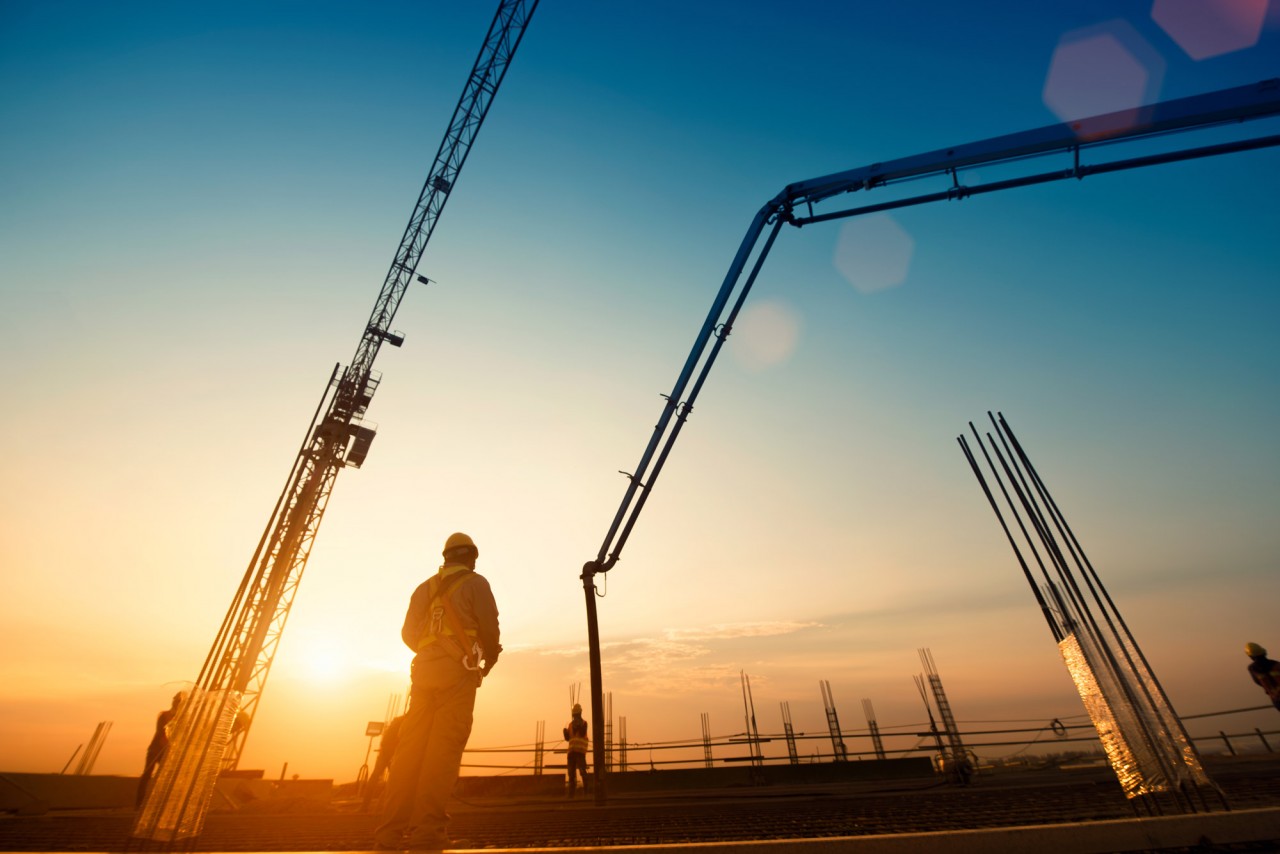
Modern construction machines must be able to perform tasks as fast as possible and with maximum accuracy.
These more accurate and safer construction machines can only be implemented through progressive automation of the machines.
The machine electronics and control technology required to achieve this are reliant on sensors that reliably output
a precise measurement value even under harsh environmental conditions.
TWK-ELEKTRONIK is specialised in this with its durable, robust and reliable magnetic rotary encoders, inclinometers and
linear transducers. Safety-relevant versions are also a standard part of our product portfolio.